Top 9 Laser Technologies Transforming Lithium Battery Manufacturing
Release time:
2025-06-30
Author:
Source:
In 2025, the lithium battery industry has seen high growth in demand across the entire industrial chain, with laser technology playing a crucial role in production processes like power battery pole piece and tab welding as well as marking for traceability due to its efficiency and quality, and it is now deeply integrating with the industry to explore solutions for more application scenarios.
According to industry insiders, since 2025, leading enterprises in all lithium battery segments have basically been in full production. From the current situation, the high-growth certainty of the entire industrial chain demand is strong. In 2025, driven by the continuous growth of new energy vehicles and the explosive demand in energy storage and other fields, the prosperity of the lithium battery industry continues to rise. With the continuous maturity of the industry and the continuous innovation of technology, a new round of dividend from the expansion of power battery production is expected to continue. At the same time, not only in the field of new energy vehicles, but also in the upgrading of 3C electronic products, lithium batteries are facing higher technical breakthroughs in energy storage. In February 2025, the Ministry of Industry and Information Technology and other eight departments issued the High-quality Development Action Plan for New Energy Storage Manufacturing, which clearly listed solid-state batteries as a key research and development direction, supported the solid-state development of lithium batteries and sodium batteries, and proposed to build 3-5 global leading enterprises before 2027. The introduction of a series of policies has injected strong impetus into the development of lithium battery technology.
Laser technology is widely used in the production and manufacturing of lithium batteries, such as laser welding for power battery pole pieces and tabs, and laser marking technology applied to lithium battery packaging tapes, casings, and other scenarios.
Application of Laser Technology in 3C Consumer Battery Tab Welding
In the production of consumer batteries, a pole piece welding process is involved to weld the battery pole piece to the current collector. The positive electrode material is aluminum sheet welded to aluminum foil, and the negative electrode material is nickel sheet welded to copper foil. After welding, the battery is formed by winding or lamination. Many packaging technologies are applied in the actual battery production process, such as laser welding, resistance welding, ultrasonic welding, etc.
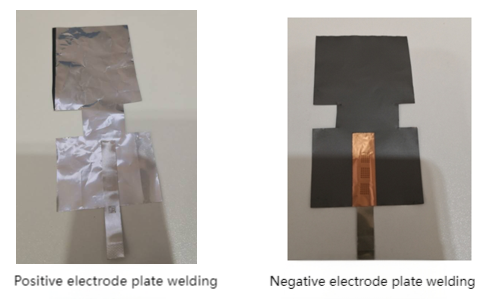
Appropriate welding methods and optimized process parameters play an important role in saving the production cost of power batteries and ensuring their uniformity and reliability. The traditional welding method is ultrasonic welding, which is prone to virtual welding, and the welding head is prone to wear. Since the wear time is unknown, it is easy to cause a large number of defective products.
Ultraviolet Nanosecond Laser Welding – Small Heat Affected Zone and Good Adhesion
Laser welding uses a laser beam as an energy source. A focusing device is used to concentrate the laser into a high-power density beam that irradiates the surface of the workpiece for heating. Under the thermal conduction of the metal material, the interior of the material melts to form a specific molten pool.
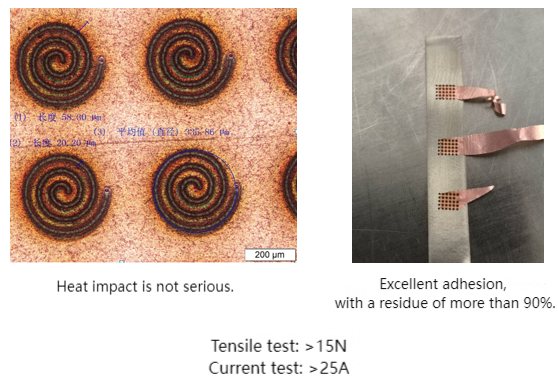
In the field of laser welding, it is further divided into infrared fiber laser welding and ultraviolet nanosecond welding. For infrared fiber laser welding, when welding the negative electrode with spiral welding, the heat affect is large; if spot welding is used, virtual welding is easy to occur. For positive electrode welding, spiral welding is difficult to achieve, and spot welding will also cause a lot of virtual welding.
Ultraviolet nanosecond welding, due to the high absorption of ultraviolet light by materials, has lower welding difficulty. It is currently the light source with the best welding effect and highest welding efficiency, featuring a small heat affected zone, good adhesion, welding efficiency of <2 seconds per piece, and a solder joint tearing residue of more than 90%.
With the in-depth development of new energy vehicles and the broad 3C electronics industry, higher requirements have been put forward for the assembly and welding accuracy and quality of supporting batteries. Nowadays, with the continuous iteration of technology, more precise laser welding technology is further integrating with the power battery field. For example, leading enterprises such as CATL have extremely high requirements for the accuracy and stability of welding technology in the research and development of new batteries, and laser welding technology is continuously upgraded to meet these needs. At the same time, the industry is also jointly exploring efficient and high-quality solutions for laser technology in different application scenarios. For instance, in the welding scenarios of large battery packs in the emerging energy storage field, laser welding technology is also constantly attempting innovative applications to meet the welding needs of large-capacity and high-stability batteries.
Laser Marking Technology – Effectively Helping Power Battery Traceability
Battery production involves multiple links, including raw material information, production processes, product batches, manufacturers, dates, etc. How to effectively achieve the whole-process traceability of lithium batteries? It is necessary to store key information in QR codes and mark them on the battery. Traditional inkjet coding technology has problems such as easy friction and information loss over time. In contrast, INNO Laser's ultraviolet marking technology has the characteristics of strong permanence, high anti-counterfeiting, high precision, strong wear resistance, safety, and reliability. It will not fade due to environmental factors over a long period, making it an excellent solution for marking in the battery industry.
Key words:
Laser Marking,Laser Welding
Prev
Prev:
Latest News
2024-07-12
HAND-HELD LASER MARKING MACHINE
2024-07-12
DIFFERENCE BETWEEN FIBER LASER CUTTING
2024-07-12
Floor 16, Building A, Rongsheng Times International, Licheng District, Jinan City, Shandong Province,China